一、 生产准备:
1、 原辅材料:
1.1、 废钢:
● 废钢的分类、技术要求、检验方法、验收规则、运输和质量说明书等满足GB/T4223 废钢铁之规定;● 废钢的块度满足《康斯迪电炉原辅材料技术操作规程》的要求;● 废钢的化学成分满足特殊钢种对微量有害元素的要求。2.1、确认康斯迪电炉机械、液压设备正常;水、气等介质供应正常;电器、计算机等自动化系统检验确认正常。● 电炉设备冷却水压力≥0.3MPa, 压缩空气压力≥0.4MPa;● 电炉变压器冷却水水压正常(0.01~0.02 MPa),油水冷却器投入运行;● 除尘风机投入运行,机力风冷器冷却风机投入运行。3.1、确认电极水冷喷淋环工作正常,发现积灰或堵塞及时处理。3.2、每炉出钢后、通电前,仔细观察上部炉壳及炉衬情况:注意上部炉壳是否有漏水现象,必须认真察看每支炉壁碳氧枪的工作状况,发现堵塞或漏水及时处理;对中后期的炉衬,要特别注意观察偏心区、2# 电极热区、炉门两侧及下部等部位的镁碳砖侵蚀情况,及时通知外包施工队用喷补料进行喷补;炉前在每次出钢后要及时清理炉门并用补炉料补筑好炉门。● 关闭EBT,对EBT进行填充,出钢口填充料应适当高出袖砖,外形呈馒头形。● 填好EBT后,摇炉回到+2。,插入电炉缓冲器,摇炉到水平位置,整理好炉门准备新一炉炼钢操作。● 新炉第一炉、出净钢水修补炉第一炉为新铺捣打料的炉坡、炉底,装料前应在炉坡、炉底铺一层薄铁板并加1~2吨石灰铺底。料罐用废钢铁料以剪切料为主,料罐停放在电炉平台下。总装入量105吨左右,全部使用废钢,不使用生铁及中重型废钢铁料,以剪切废钢为主;出钢量70吨左右。新炉装料先用料罐分批加入废钢,至装入量达到70吨后启动康斯迪加料,从康斯迪加入废钢约35吨;修补炉用料罐加入30吨废钢以后方可启动康斯迪加料。
总装入量110吨左右,钢铁料配比:废钢80%左右、生铁20%左右,出钢量70~80吨。先加入30~40吨废钢,溶清后启动康斯迪加料。康斯迪料槽中加料高度控制500mm左右,最高应小于700mm。 总装入量80±5吨,钢铁料配比:废钢70~80%、生铁20~30%。出钢量70~80吨。● 炉内留钢量在正常生产时应保持25~35吨,根据电炉炉龄和实际生产情况可作调整。留钢量少于10吨时,必须先用料罐或康斯迪加入废钢使炉内装入量达到25吨以上才能通电冶炼。在电炉回到水平位置后,连接小车到达“EAF”位,启动连接加料小车及康斯迪输料道开始直接往炉内加钢铁料。 1/3的生铁在炉内装入量85吨以后时加入,2/3的生铁在电炉通电后从康斯迪料槽加入,在装入量达到60吨前加完。生铁的加入量一般为15~30吨/炉,可根据冶炼钢种和废钢机械生铁含量的不同及对有害元素的特殊要求调整生铁的加入量。 主要由南康斯迪行车加入康斯迪料槽,南康斯迪行车故障时用北康斯迪行车加,要求生铁在康斯迪料槽内分布要均匀、撒开。正常情况石灰的总加入量为3000~4000Kg/炉,白云石的加入量1000Kg/炉。根据钢水中P、S含量进行调整。 新炉、中修炉第一炉:石灰加入量4000Kg左右,不使用萤石、白云石。在进料罐前先加入1000~2000Kg石灰;在康斯迪加料时再加入约2000~3000Kg石灰。石灰的加入量3200Kg,白云石的加入量1000Kg,通过石灰加料系统加入康斯迪料槽。分4~5次加入,每次800~1000Kg,分别于通电开始、炉内45吨、炉内60吨、炉内75吨、炉内90吨等时段加入,炉内熔清后如熔清样磷含量高,可由高位料仓补加石灰。萤石作为调渣材料,其加入量应根据炉渣粘度决定,确保炉渣具有良好的流动性,禁止过量使用。
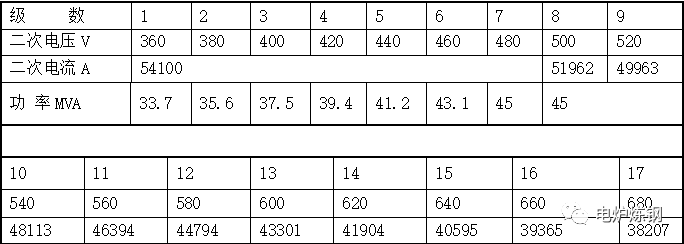
装第一批料,以8~10级电压手动供电,熔清后停15~20分钟后加入第二批料,再以8~10级电压手动供电,熔清后停15~20分钟左右后加入第三批料,以8~10级电压手动供电;基本熔清停30分钟左右后启动康斯迪加料,以10~13级电压手动供电。如因料罐小,进料次数多,熔清后的停炉时间可以适当减少。新炉第一炉的冶炼时间大于210分钟;修补炉第一炉的冶炼时间大于150分钟。 装第一批料,以8~10级电压供电,熔清后加入第二批料,以10~13级电压供电,基本熔清后启动康斯迪加料以15~17级电压供电。 当电炉回到水平位置后,启动康斯迪加料,根据冶炼进度、炉内温度和泡沫渣情况,控制合适的加料速度及供电曲线,一般以15~17级电压供电。冶炼中造好泡沫渣,做到埋弧操作,控制供氧强度,避免大沸腾现象发生。注意:电炉在生产过程中尽量避免有载调压!调压时提升电极,至电流归零,再调电压。● 跳电:在冶炼过程中,遇到电流波动过大(如塌料等),会产生跳电现象,跳电炉高压开关只要在主控室按“复位”按钮解除即可继续合闸生产;如跳33KV或220KV,则必须通知电工处理。● 允许合闸指示灯不亮:检查“F7”供电条件是否满足。碳粉喷入量设定范围为20~50 kg/min,以确保炉内泡沫渣良好为宜。氧气流量设定:小流量――1500~2000Nm3/h;大流量――3500~4000Nm3/h, 在第一、第二、第三批料熔化过程中不进行吹氧,第三批料熔化后,用碳氧枪小流量吹氧,同时视情况喷少量碳粉造泡沫渣。启动康斯迪后,增大碳粉量,氧气流量控制在小流量,碳粉喷吹流量控制在20Kg/min左右。 先启动水冷碳氧枪往炉内小流量吹氧喷碳形成泡沫渣后,再通电进行正常的冶炼操作。根据炉内钢水量确定氧气流量;装入量未达35吨之前用小流量供氧,35吨后用大流量供氧。确立先进枪后通电的原则,废钢未进到炉内不得使用大流量氧气供氧;熔池温度低时碳氧枪以造泡沫渣为主,泡沫渣造好后碳氧枪以切割废钢为主。 控制好炉内渣量,适量适时流渣,造好泡沫渣,埋弧升温。注意:根据配碳量、废钢情况和实时炉况合理控制氧气使用流量及枪位,防止钢水过氧化及大沸腾。3.1.1装入量接近和达到目标值 ,便进入升温阶段,当熔池温度达到1550℃左右时取第一个样作全分析,(如果炉内进有冷钢则要等冷钢基本熔化再取样);根据分析结果决定是否取第二个样。如果第一个样成分符合工艺要求,至熔池温度达到1580℃左右时取终点样;如第一个样〔C〕高,吹氧脱〔C〕后再取第二个样分析;如果〔P〕高,流渣后补加石灰和适量萤石造渣脱〔
P〕后再取第二个样分析,成分合格后至熔池温度达到1580℃左右时取终点样。在低合金钢的生产中为了有害元素的控制是一项基本的要求,一般包括:Cu、Ni、As、Sb、Sn、Pb、 Bi等,大多来源于废钢,为了控制微量有害元素的含量,尽量地降低损失,要求做到:● 在电炉熔清时发现微量有害元素超标则立即与储运调度联系,通知情况,并请储运调换废钢。● 对于已经送到康斯迪料场上的废钢必须与储运后送的废钢搭配方可入炉。● 对于电炉炉内已经发生的微量有害元素超标的情况,电炉出钢时必须尽量多倒出炉内钢水,请示领导处理。● 当班发生的微量有害元素超标的情况必须在值班记录上清楚反映,避免事故的重复发生。由于变压器输出功率和化学能相对稳定,溶池温度控制主要由康斯迪加料速度决定,为了保证溶池温度在碳沸腾温度范围,特殊能量控制在280~320Kwh/t为宜,此时炉内的钢水温度在1530~1580℃范围内。炉内钢水量达到目标值90~95%时,减慢康斯迪加料速度,提升溶池温度,并进行取样、测温操作。炉内钢水量达到目标装入量后,停止加料。● 合金加入量在1.2吨以上的钢种温度提高20℃,如果Cr铁、Mo铁加入量大,再提高20℃;● 冷炉、全新钢包、备用钢包等视情况温度各提高30±10℃。⑴、连接小车退出到“OUT”位,退出炉门碳氧枪;停电并将电极操作手柄打到“出钢”位置,摇炉控制权转移到炉后出钢操作台。以下在炉后出钢操作台上进行:⑵、电炉倾动到+2~5℃,打开EBT,如填料不能自动流出,可用氧气引流。⑶、当包内钢水5~10t时,随钢流将配好的精练渣、铁合金加入钢包内。铁合金的加入量以达到各钢种的合金成分下限为准,具体加入量可参考各钢种的《工艺操作要点》;精练渣加入量为10Kg/t钢。⑷、出钢量依据钢包车上的称量系统控制目标70-80t钢水,如称重系统故障,可依据倾炉角度从5°、9°、15°控制,各位置均有设定的出钢量,同时根据钢包内钢水液面以及钢包的包龄估计钢包中的钢水量。⑸、出钢量达到目标值时(目标值要随着钢包的状况随时调整),快速摇回电炉至-7°,同时启动钢包车退出,以防止氧化渣倒入钢包。
⑴、在冶炼Q215、Q235等普碳钢时在出钢时只加入0.5kg/吨钢铝饼进行预脱氧;⑵、在冶炼优钢、特钢时在电炉出钢时加入0.5~1.0kg/吨钢铝饼进行预脱氧;5.1 冶炼前期与正常操作一样,减少生铁加入量,炉内装入量控制在70t左右。为便于检查康斯迪设备,康斯迪料槽内的废钢料要走清。5.2 熔清后尽量流掉炉渣,使炉内渣量降到最低程度。5.5 炉中剩余的钢渣倒在备用钢包里,倒去上层氧化渣,剩余钢水倒入精炼炉钢包中。5.6 出钢完毕,检查出钢口,将水口下的残渣清理干净。关闭EBT,填好出钢口,摇平电炉,开始进入下一炉冶炼。● 炉前处理炉门专用叉车指定专人驾驶;配电操作由主操或付操作工操作。